News
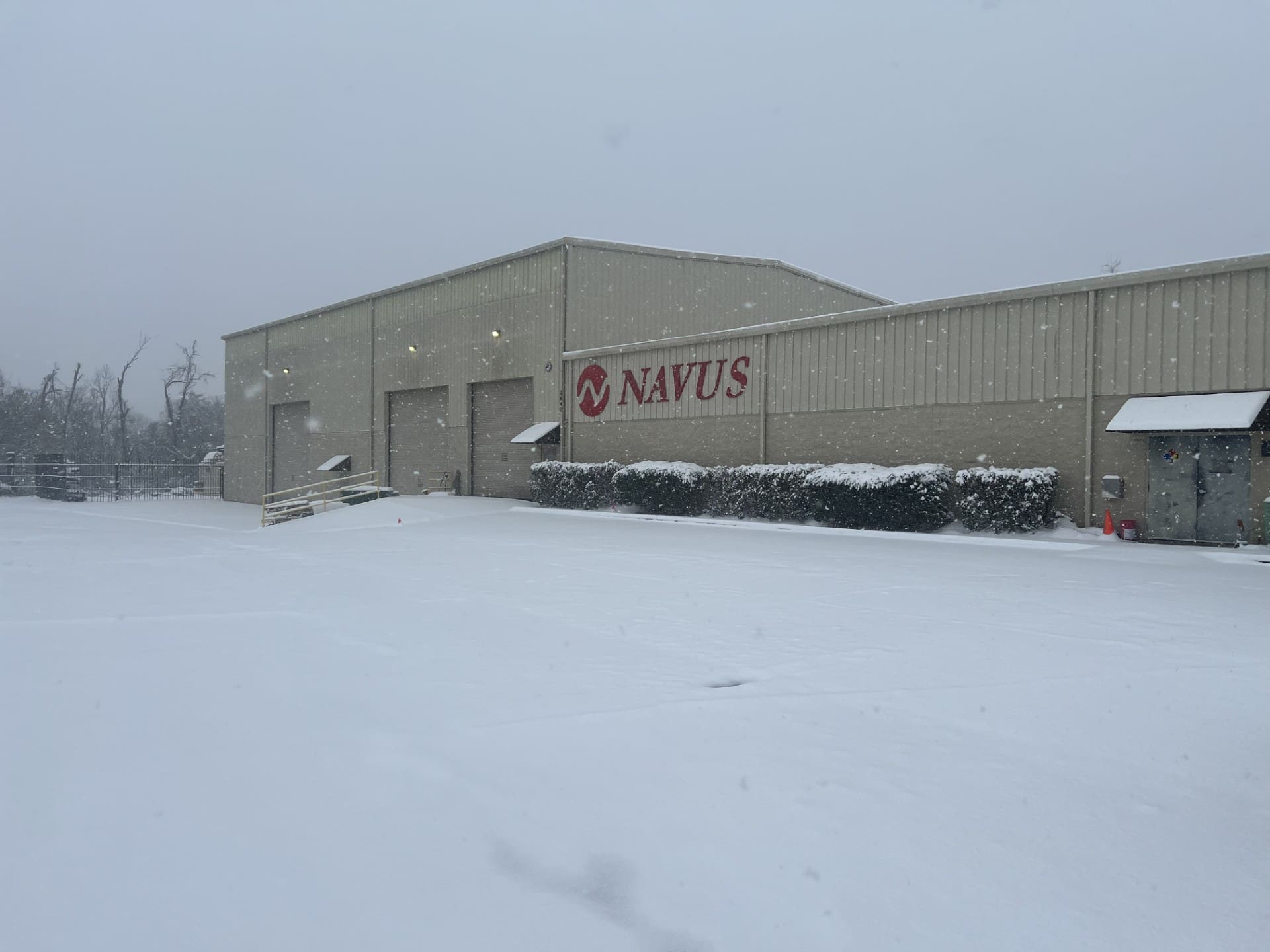
Navus Quarterly Newsletter
01/01/2025 Q1 | NAVUS
Service department and Procurement Changes
As we enter into the new year we are both sad and excited for Ryan Gallagher as he has parted ways with Navus to pursue other career opportunities. Ryan has been a huge part of the Navus team in the past few years but we are excited for him as he takes on these new challenges.
Suppliers, don’t get too excited… your new contact will be Parker Richardson, and we expect he will be just as hard-headed and tenacious as Ryan. Parker has been with Navus for a couple years, spending much of his time training with Ryan to take over his position in procurement. Feel free to reach out to him at PRichardson@navusinc.com.
*Customers, don’t be too sad, you now have Tanner White to help out with all service department needs. Tanner is a new employee here at Navus that we are super excited to have him on our team. He was able to train with Ryan on the service side of things and now has the whole Navus Team backing him up. Tanner has a background in mechanical engineering and business administration and we look forward to seeing how he is able to help shape and grow the future of Navus. His contact is TWhite@navusinc.com but feel free to reach out to service@navusinc.com for any service inquiries.*
Parker Richardson Tanner White
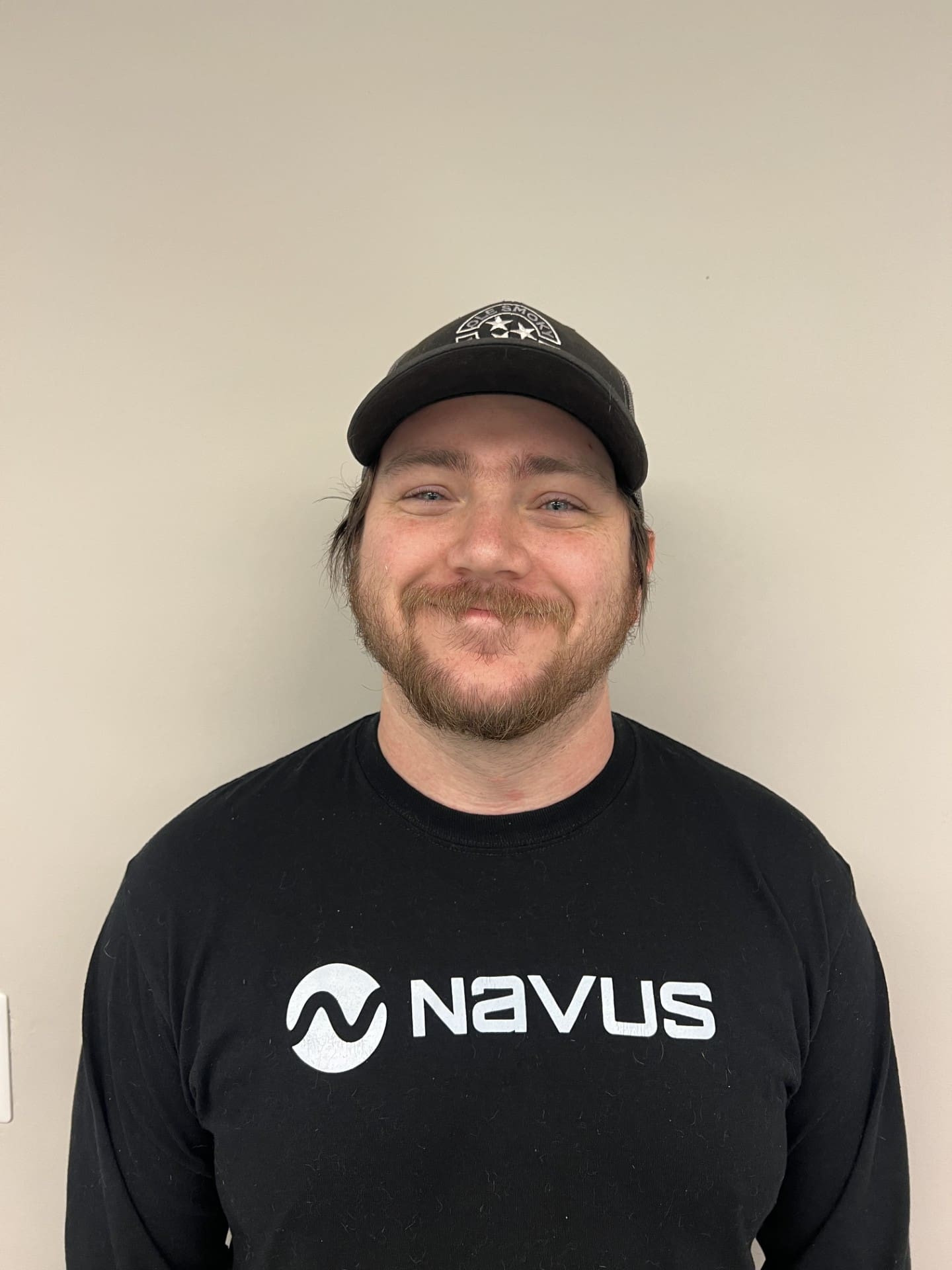
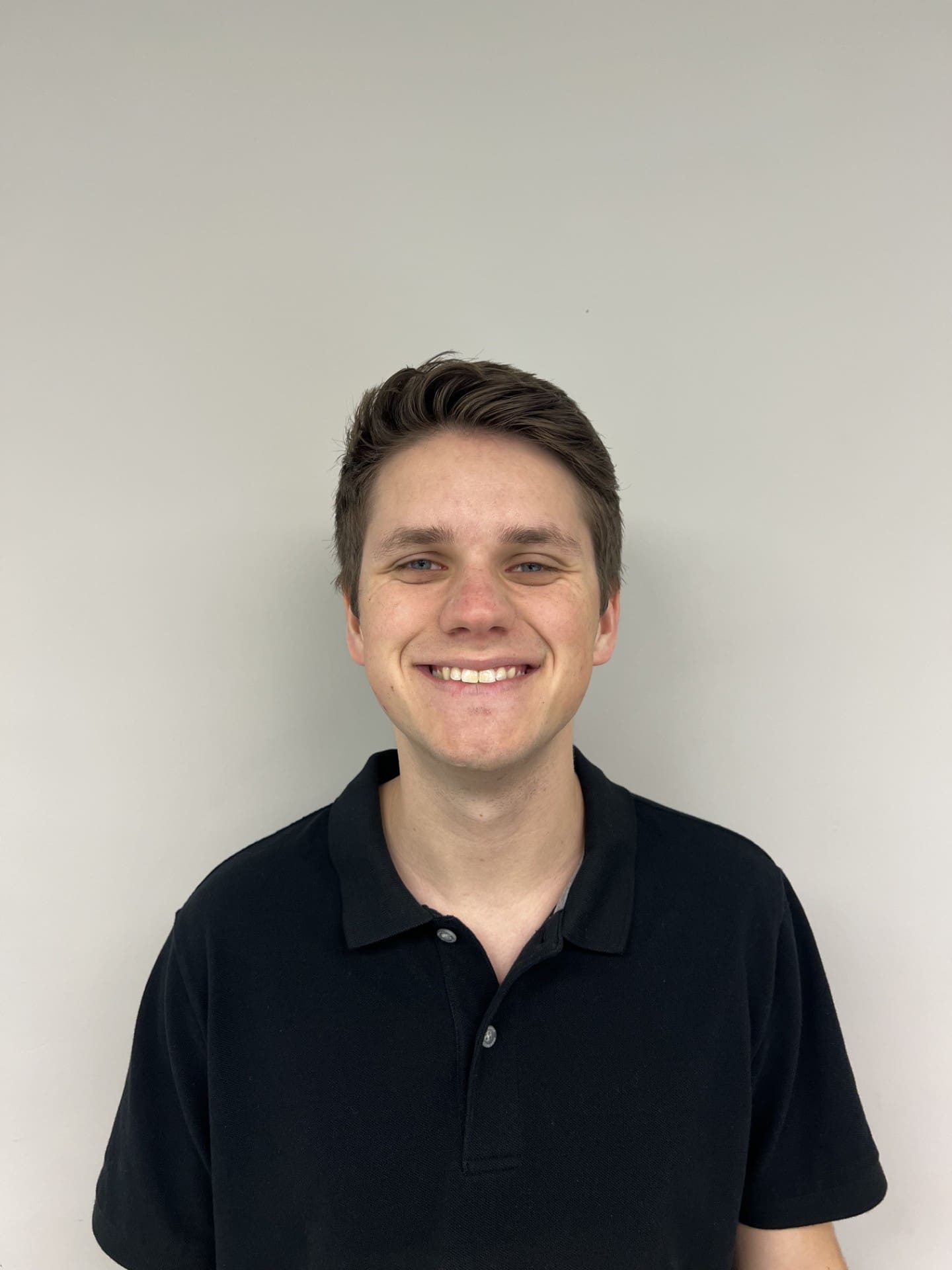
New Project Spotlight
*Navus is currently taking on a new challenge in the form of a 5-robot high-speed assembly and packaging line! The robots will consist of 5 Fanuc robots; (2) SR6IA scara, (1) SR12IA scara, M-20ID/35 6 axis, and (1) DR3IB8L delta. We are very excited to take on this new challenge for our customer. This machine will include a complete start-to-finish process. This machine will include some ink-jet barcoding, part feeding, assembly, and screwdriving on the front end. On the back end we will have case erecting and sealing along with adding labels and scanning to log what has gone through. The final station will be palletizing. This system is truly a start to finish process! At Navus we pride ourselves in being able to find a complete and full solution that fits our customer’s needs. *Our amazing team of engineers and technicians are able to help advise and provide the best and most efficient automation solutions that are tailored exactly to our customers' needs. We are looking forward to the next phase of this project and what’s to come in 2025.
Employee of the Quarter
Navus Employee of the quarter goes to none other than Mason McNutt! Mason has been with Navus for _ years in the mechanical engineering position. Mason is an invaluable member of the team and someone who is truly unforgettable. If you have had the pleasure of meeting or working with Mason you probably know him for he endearing charm, large stature, and quick witted comments. Mason’s strengths come in the form of creative ideas, excellent ability to find problems on our machines before we send them, technical skills, and his ability to make people laugh. It has been a pleasure working with Mason and we are so excited to see what he is able to accomplish this year!
Quarterly Newsletter: Exciting Updates at Your Automation Integration Partner
New Service Department
At Navus Automation, we’re committed to not just delivering cutting-edge custom robotic automation solutions, but also ensuring their continued excellence throughout their lifecycle. That’s why we’re thrilled to announce the launch of our brand-new Service Department, designed to keep your systems running smoothly and efficiently.
Why the New Service Department?
Our dedication to your satisfaction and operational success extends beyond the installation of your custom machinery. We all understand that even the most advanced systems require ongoing support to maintain peak performance. Our new department is here to provide that crucial support with a comprehensive range of services:
Repairs and Maintenance: Whether it’s routine maintenance or unexpected repairs, our expert technicians can come to you and get it done.
Custom Spare Parts:Â We manufacture and source a wide range of high-quality spare parts tailored specifically to your machinery, we want to minimize your downtime and maximize your productivity.
Troubleshooting and Support: Encountering a problem? Our experienced engineers are masters at diagnosing and resolving issues efficiently, we’ll find the right knowledge base to solve your problem.
Upgrades and Enhancements: Looking to boost the performance of your existing systems in a fast-moving world? We offer solutions for upgrading and enhancing your machinery to keep you at the forefront of technological advancements.
How to get in touch!
At any time reach out to service@navusinc.com and someone will reach out to you as soon as possible!
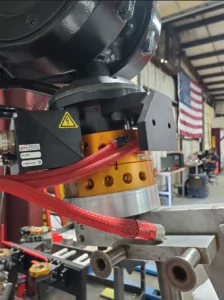
Project Spotlight
Building Apps That Teach Robots to Weld
Do you ever need high-quality welding for a project but lack the necessary personnel or tools?
Mike Teubert, our Senior Robotics Engineer, and Certified Welding Inspector, is developing innovative applications for the ABB GOFA Cobot designed to simplify the welding process. These Teach Pendant Apps enable individuals with no prior welding experience to achieve professional-level results effortlessly.
By simply entering the material thickness and specifying the start and end points of the weld, users can swiftly produce high-quality welds. The system allows for fine-tuning and automatically corrects for suboptimal angles, ensuring consistent results. No programming knowledge is required—just straightforward operation and excellent outcomes.